Checklist: How to Manage Your Own Steel Building Project
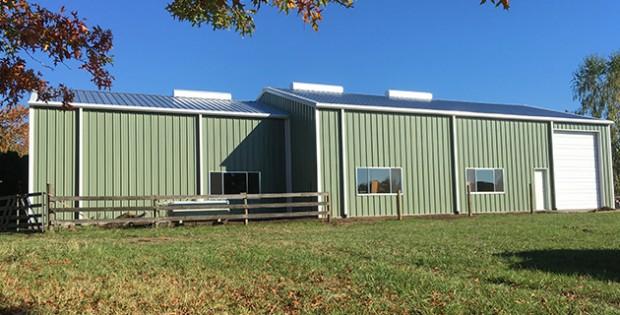
Pre-engineered metal buildings are a do-it-yourselfer’s dream. Even if you don’t consider yourself an experienced builder or a qualified handyman or woman, many people manage a steel building project themselves every day. That’s not to say they don’t get help when they need it! Let’s face it – construction projects of all types have the potential to be expensive. Shouldn’t you look at cost saving techniques at every avenue? Do you need everything that someone tells you that you need, or can you really accomplish the goals of a steel building project by yourself?
We’ve put together a list of essentials for you to be able to manage all the finer aspects of a steel building project, while saving money and getting the most out of your budget.
Know the specifics of your steel building project
Do you have your finances in place? It’s extremely important to understand your budget – and the factors that determine the price of your steel building. Generally, first time builders receive huge savings on the price of steel and steel building accessories when they are able to go through the Direct Buy process.
Do you know the dimensions you want? Pre-engineered metal buildings are sold according to their width, length and height. With so many different design options, builders should have a good idea of dimensions or square footage before beginning. One big checklist item you can cross off the list early: call your local building authority. It’s vital to know about your property zoning laws or any homeowner’s association rules or requirements. For example, some customers live in elevation dependent locations. In parts of the same county, literally only separated by 10 miles, elevations can be extremely different. This affects the loads and codes of a pre-engineered metal building. By speaking with your local building authority, you’ll be able to get all the necessary information for you to obtain accurate steel building quotes.
Skip the Architect
Many builders – especially ones who manage their own project – automatically assume they need to get drawings from an architect before they begin. But that’s not always necessary. While it’s true you’ll need to obtain drawings (blueprints), often you can procure those drawings from a steel building supplier, like Armstrong Steel. Architects are extremely talented and produce beautiful work, but as drawings get more complicated, the price goes upwards. Architects also can offer further exterior development and construction documents, but your steel building manufacturer can also provide those elements. If you’re designing a workshop, garage, barn or commercial building, generally you can skip the added expense of an architect and obtain your drawings from a steel building supplier for much less.
Take advantage of factory direct pricing
This is the key item to managing your own project. Up until recently, the only way to get a steel building was through a contractor or a steel building broker. But now, you have a third and more cost effective option, which is to buy a steel building directly from the factory. No longer will you have to go through a broker, who is essentially an expensive middleman. You want to manage your own project, not be subjected to the whims of a middleman! Instead of letting a broker choose the lowest quality building and accessories, you can manage your budget by making those selections yourself from a manufacturer’s special components catalog. With the Direct Buy process, you’ll be able to mark up your drawings, add openings and accessories and fully customize your project with the help of a dedicated project manager. Don’t worry, you’re still in charge of your own project, and your “project manager” is in place to serve as a go-between you and the engineering team at your steel building supplier. Project managers work at our corporate offices and are assigned to each project and their expertise is included with your steel building purchase. Once the project manager receives your requested changes and estimates your costs on accessories, you’ll accept or continue to customize your project, and then schedule your delivery and eventually erect your building! For a more in depth explanation of the Direct Buy process, click here!
Choose an appropriate timeline
You’re not getting a steel building off the shelf, or one that’s already constructed and waiting in some stock yard. You’re getting a fully customized structure, engineered for your exact specifications. That being said, it’s imperative that you allow yourself time for the design and scheduling process. While it can be lengthy, there are several steps you can take so the permitting process doesn’t derail your timeline.
Erect the building yourself
Many first time builders who choose to manage the steel building project themselves usually erect the building themselves too. If you decide to farm out the work to a professional, you’ll have to pay a construction crew to erect the building, along with a general contractor to manage your project. There is nothing wrong with hiring a crew and a general contractor, and it might be a necessary expense if you have a bigger steel building project. Building material from Armstrong Steel arrives with holes pre-punched and components are pre-cut and numbered to correspond perfectly with your construction drawings. It’s the ultimate do-it-yourself project.
Use this checklist to save yourself time and money by managing your own steel building project. Click here to see examples of other builders who have managed their own steel building projects to success!
« Why do Clinton and Trump Keep Bringing Up Foreign Steel?
3 Reasons Why Steel is the Most Cost Effective Building Solution »
Popular Posts
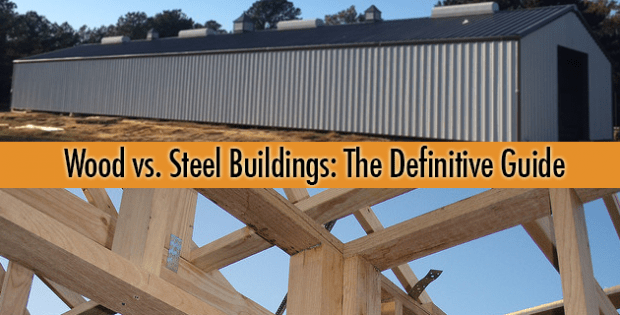
Wood and steel buildings are both widely used construction materials but there are many differences between the two. How do you decide on a wood pole barn or a pre-engineered steel building? There are several things to consider when selecting the best-fit building material for your new structure. Whether you are building a garage, workshop,… …
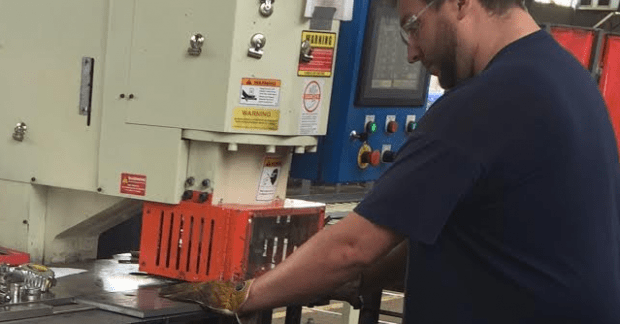
You’re faced with a decision and it’s one you might not have even considered. You’ve made a choice to buy a building for your property, your farm, your small business, your church – a workshop, a garage, a place for storage. Your mind is flooded with important decisions. What do I want? How do I… …