Best Practices Guide for First Time Steel Building Buyers
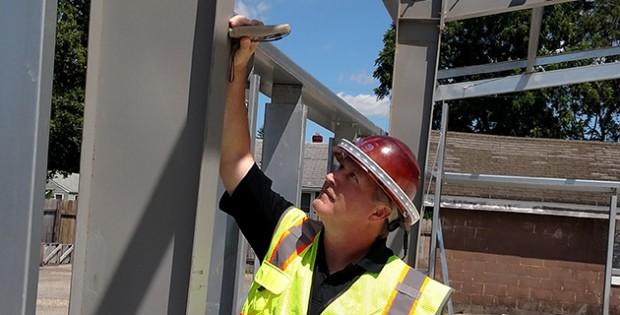
Every day, I get to begin construction projects with builders across the country. It’s just an exciting prospect to listen to enthusiastic do-it-yourselfers and construction professionals who are on the verge of adding a new workshop, agricultural or commercial building to their property. For some, including many first time builders I’ve spoken to, a building project can be incredibly daunting. I can understand the apprehension of a construction project, especially one where you get to manage some of the finer details. Armed with a little knowledge, you can be sure to make your steel building project a success.
A little bit of homework goes a long way
Pre-engineered steel building systems are complete, integrated set of mutually dependent components and assemblies that form a building, including primary and secondary framing, covering and accessories. They are engineered for your exact area and building specifications. In order for engineers to accomplish this task, they must know those numbers, as well as your building address. This can be solved by a simple phone call to your local building authority. Knowledge of all your own personal zoning by-laws, rules and regulations of your homeowner’s association, or permit requirements can help make the process smooth throughout, as well as gain an accurate quote.
Purchase from a steel building manufacturer
The best practice – which equates to getting the highest quality structure for your money – is to buy from a steel building manufacturer. You might assume that every company that sells steel buildings are manufacturers, when in fact, this isn’t the case. A manufacturer actually fabricates its own product. They’ll also be able to design and engineer their own product without involving a middleman. A steel building broker is essentially a middleman between you, the potential builder, and a steel building manufacturer. A broker will shop your building design around to manufacturers and then buy it from the highest bidder, while paying little attention to quality. Many times, they’ll buy the cheapest building, regardless of who makes it, mark it up, and pass the engineering and design to others. Brokers are often times only in the business of outsourcing and finding the cheapest price to maximize their own profits. Purchasing from a broker could open you up to cost increases, or worse, a cheap building that doesn’t last.
Budget correctly
What can you afford? As a whole, pre-engineering steel building projects are usually half the cost of building projects that utilize traditional construction materials, such as wood or brick. Steel buildings can also be erected in days or weeks, not months like those wood applications. Plus, since steel buildings are made of the most durable construction material on the planet, you don’t have to break the bank right off the bat. Rafters, roof panels and support beams don’t require a replacement every few years on a steel building because they are constructed to last. Wood is biologically predisposed to decay. Steel will last for generations. While a steel building might require a great initial investment, you’ll likely spend more money over the structure’s lifetime if you choose to build a wood pole barn.
Choose your own accessories
Steel building accessories give each building a custom look and function. Accessories are defined by Armstrong as products that are not included as part of the basic steel building system. Accessories commonly include components such as doors, windows, canopies, vents, gutters, downspouts, skylights, cupolas and more. If you can take advantage of the Direct Buy process, you’ll get to choose your own accessories for your steel building purchase. Why is this significant? By choosing your own accessories, you ensure your project stays within your budget. You’ll have access to Armstrong’s Direct Pricing Catalog and receive special pricing not only for steel, but on those building components too.
Prepare your job site
Erecting your pre-engineered steel building can be done in as little as a few days or weeks, but you’ll need to take care of a few tasks while you wait for it to arrive. Before you can erect your building, you need to prepare your job site. That usually starts with land grading and a foundation. The best time to lay your foundation is during a warm season. You can lay a foundation during the winter, but your risk of making a mistake increases. Your cement could freeze before the curing process is finished, which could crack your foundation due to frost heaving. Your foundation is what you’re pre-engineered steel building rests on, and if your foundation is compromised, your pre-engineered steel building won’t stand much of a chance.
Did you get the proper permits? If you didn’t, you might not be able to erect your building on the site you planned. It might not be possible to change locations for your pre-engineered steel building because it’s designed specifically for your area. Designers take wind loads, snow loads and seismic activity into consideration, and you may not meet the proper requirements to erect on a different site. Once your foundation is laid and you have all of the proper paperwork signed, you’ll schedule your delivery. A set of directions will come with your pre-engineered steel building and they’re vital to a successful steel building project. Don’t forget about site planning, survey and making sure your site is accessible for delivery trucks. Be sure to have a forklift on site to unload your building too!
We’d love to hear from other builders! What would you consider a best practice? Start the conversation below!
« Leveraging Factory Direct Pricing for Your Steel Building Project
Get More Out of Your Steel Building Budget »
Popular Posts
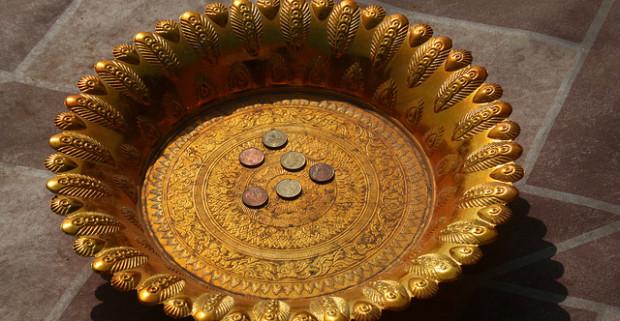
The time has come to raise money for your church and money isn’t an easy thing to ask for. Church renovations, erecting a steel building for the youth group or sending a missionary group out of the country all cost a lot more than you would think. Asking for money from your church is hard…. …
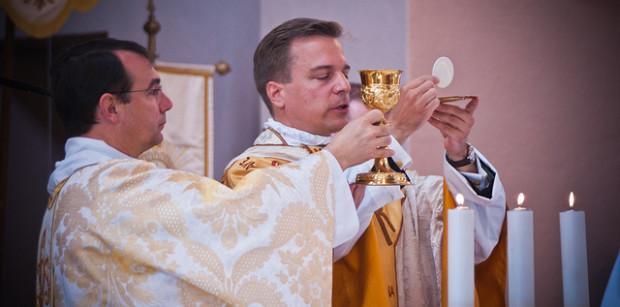
Often times, as I design your steel building, I’ll take a look at some of my past designs. Because of different building loads and codes, every building that goes through our rigorous engineering process is unique and built to your exact specifications. But that doesn’t mean that I can’t go back and admire some really… …