Buyer Beware: Watch Out For These 3 Steel Building Red Flags
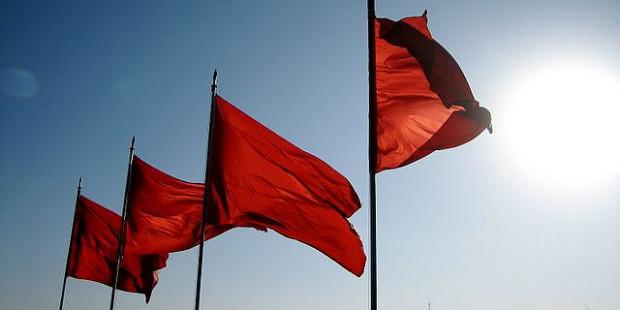
Whether you’re looking to buy a commercial steel building or a workshop for your backyard, purchasing any kind of metal building is a big investment. Not only that, but there’s an emotional component to big financial acquisitions. As a buyer, you must look through all the sales and marketing mumbo jumbo to truly see the real integrity of a steel building provider. That’s where consumerism becomes tricky. What do you look for when you shop? Regardless of who you buy from, pay attention to these potential red flags when shopping for a steel building. Keep in mind, the term, “red flag,” doesn’t mean absolutely, positively, avoid at all costs. However, it should still raise some concern. I always recommend that you stop and think about your choice and how it will impact your personal situation.
Cheapest Building
There are a few ways to help you get the best possible price on your steel building, but buying the cheapest building available isn’t one of them. Cheap buildings potentially come with parts missing or holes that don’t line up because they were fabricated in a factory where speed, not quality, was the end game. In the construction industry, you truly get what you pay for. The cheapest buildings are the cheapest because companies don’t follow industry standards, and only look to pad their own bottom line. Savings in production costs doesn’t translate to savings for you.
Who sells cheap buildings? Steel building brokers can offer a cheap deal, with no concern for future costs. What about design and engineering? And those same brokers might leave the engineering to others and have less incentive to placate any warranty claims. When it’s all said and done – meaning the building is erected on your property – the cheapest building could end up being the most expensive because of labor costs, construction delays, and poor quality.
“All-Included”
Who doesn’t want everything included? When you’re buying a car, you’re told, ‘all-included,’ means that Bluetooth, power locks, air conditioning, and all the extras are lumped into the price. You don’t bat an eye. Why is that? Those accessories are what’s expected and common in new cars, and usually don’t significantly increase the price. But ‘all-included’ in the steel building industry is a little different, and here’s why.
Steel building accessories can be expensive, and steel building brokers and contractors selling turnkey buildings know it. You want to be able to select your own doors, windows, gutters and other add-ons, and have a say in what goes on your building. If you let someone pick these accessories out for you, you might be in for extra markups that you didn’t even know existed. Don’t let a building salesman pick out your doors and windows for you. It’s a big red flag if a provider won’t let you make your own selections. How do you know if you’re getting scammed or not? Would you buy a house without knowing what color it was? A steel building provider should offer you the option to manage these certain aspects of your own project.
Over-ambitious Delivery Options
A steel building isn’t a Blu-Ray player. It’s not a set of pots and pans, nor is it a speaker system for your truck. It doesn’t arrive to your property in 4-6 business days after you order it. You need to be flexible with your delivery schedule. It’s a huge red flag if any steel building provider is way over ambitious with delivery options.
I don’t have a problem admitting that the process of a steel building purchase, from conception to completion, takes time. If you decide to buy a steel building, your project won’t hit a project manager’s desk until engineers draft and provide drawings for your job. Then you’ll go through the Direct Buy process, where you can design and pick your accessories (remember from earlier?). You might have changes you’d like to make in this process. Then you’ll have to ‘OK’ a set of revised approval drawings. After that, you’ll take your engineering drawings to your county for permitting purposes. The county will verify wind, snow and seismic loads. I’m sure you’re starting to get the picture, and I haven’t even brought up fabrication yet. A meticulous effort must be provided in order to guarantee your building stands for decades, or longer. In the fabrication stage, holes must line up and parts fit together perfectly so you can erect your building with ease, the first time, the only time.
Be wary of steel building providers that say they can get you a steel building in a matter of weeks. Even if it’s possible, do you know exactly what you’re getting?
Most times, you can work with the shipping and logistics department to work out your freight plan and delivery schedule. In reality, if you can be flexible with regards to your delivery date, there might be a big opportunity to save some money through freight consolidation.
Keep in mind: the amount of time spent on each project will vary from person to person. While the entire process can be lengthy, it’s in place to guarantee you get precisely what you want.
Can you think of any more red flags? Join the conversation below!
Photo courtesy: Alfred Smith« Are You Working with Green Materials?
Your Steel Building Questions Answered »
Popular Posts
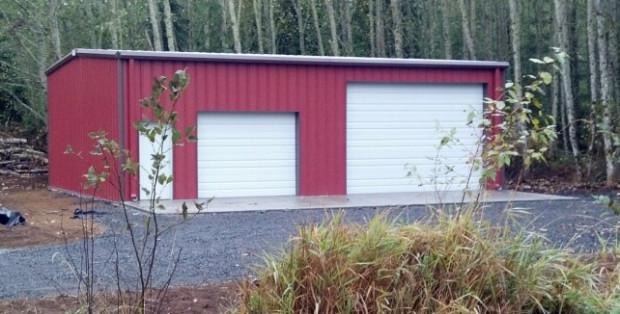
There are benefits and drawbacks for both rigid frame and Arch buildings. Not all custom steel buildings are alike. Depending on what your needs are, you may fare better with an arch frame rather than a rigid frame. Rigid frame architecture has excellent value because you can utilize every square inch of your steel building… …
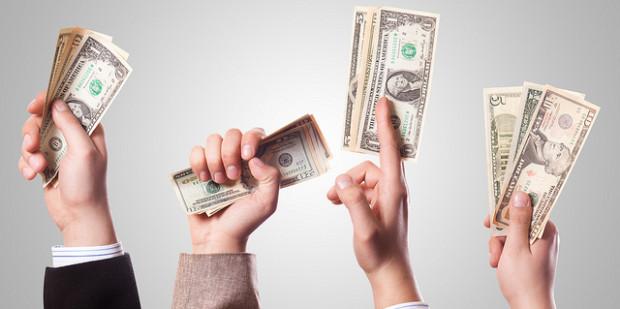
Whether you’re looking for a new sturdy barn for your farm, a place to park your classic cars and trucks, or a space to work on your hobbies and pet projects, a steel building is the complete solution to your desires. As with any purchase, you’re looking to get the most for your money. Since… …